Processors, such as the CPU and GPU in a computer system, are made up of digital gates, which are nothing more than discreet transistors that open and close, allowing the flow of electricity to pass through.
There are literally millions of these gates in a processor, operating at extremely high frequencies, which is what causes the heat to be generated. In order to assist in transferring this generated heat away from the processing unit, each processor has a metallic Integrated Heat Spreader (IHS) physically bonded to its die (on which all the circuitry has been fabricated).
From the IHS, heat is then transferred to the baseplate of a CPU/GPU cooler, which adopts one of two approaches to distribute and dissipate the heat: liquid cooling or air cooling.
Air Cooling vs Liquid Cooling
The aim of both air and liquid cooled solutions is the same, namely, to transfer heat away from the processor and maintain the temperature within operating specifications.
Both solutions have a baseplate that is physically mounted to the processor's IHS with the use of thermal paste, ensuring that there are no air gaps in the connection between the two surfaces, which can dramatically decrease heat dissipation efficiency.
It is the way in which the heat is then distributed, dissipated, and cooled that differentiates the two solutions, differences that can make one or the other more suitable for a specific situation.
Air Cooling

Air cooling is the more prevalent cooling solution on desktop and laptop systems. It comprises a metal heatsink with an array of fins. Heat pipes are used to efficiently transfer heat from the cooler’s baseplate to the fins, where a fan can further assist the cooling process by blowing or drawing air across the fins and ideally out of the enclosure.
The key component in an air cooler is the fins; Heatsink fins increase the surface area over which air can flow and dissipation can occur. The greater the surface area, the better the heat dissipation achieved. As stated, a fan creating an airflow over the fins is then used to further increase the effectiveness of an air cooler.
However, not all air coolers use a fan. Passive air coolers rely entirely on the efficient design of their fins. Not having a fan makes these coolers silent. But fanless may not always be enough, especially on high end CPUs and GPUs which draw large amounts of current, particularly under heavy, processing intensive applications, as in the case of computer games. In such cases, one and even two fans may be required.
The materials most commonly used in air coolers are aluminium and copper, with aluminium being the more widespread, due to its lower cost. Copper being a better conductor than aluminium however, is very often found in the baseplate, where maximum heat transfer is required and is also the material of choice in more high end air coolers.
Liquid Cooling
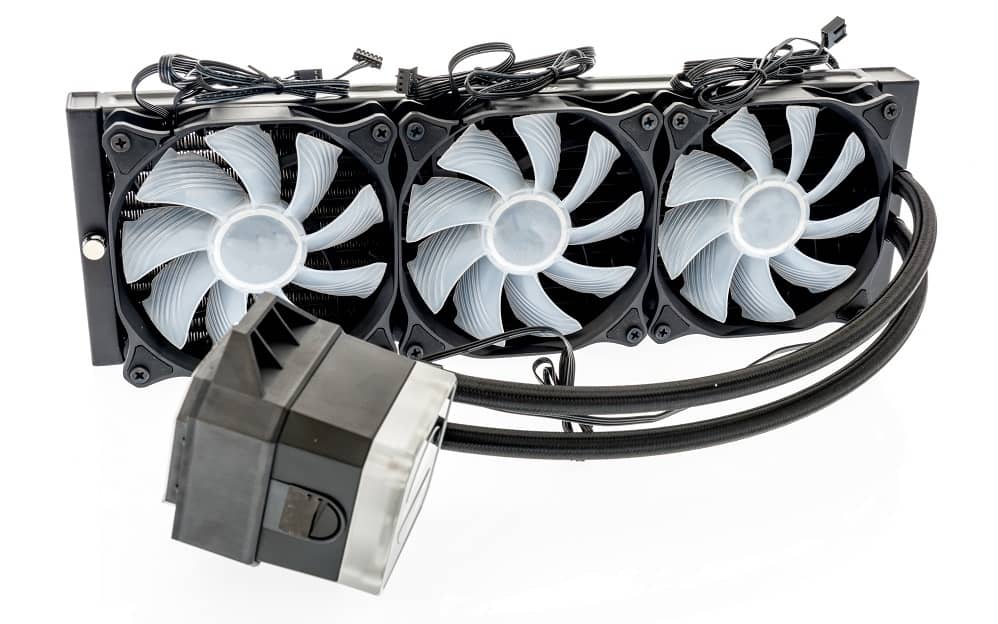
Liquid cooling is similar to air cooling, but instead of a baseplate and heat pipes transferring heat to a heatsink’s fins, a metal cooling block filled with coolant (usually distilled water or water mixed with a coolant additive), are used.
The cooling block is mounted to the processor's IHS via its baseplate, transferring any absorbed heat to the coolant. A pump circulates the coolant in a looped configuration using tubing, drawing warm coolant away from the cooling block and through a radiator, where it is cooled and circulated back into the cooling block.
A fan or fans are used to cool the coolant as it passes through the radiator, the principle being similar in manner to the way fans draw air across the fins of an air cooled heatsink to dissipate heat. This is also the way a radiator and fan in a car operate, circulating coolant through the engine block and absorbing any heat, which is then cooled as it passes through the radiator.
As with standard and passive air cooling, liquid cooling solutions also come in two flavors: All-in-One Liquid Cooling and Custom Loop Liquid Cooling.
All-in-one (AIO) liquid coolers comprise the radiator, and cooling block & pump combo, all connected with tubing in a closed loop. The cooling block and pump come as a single unit and are mounted to the processor via the cooling block’s baseplate (and thermal paste), while the radiator with its fan or fans are mounted to the computer case or chassis.
Custom loop liquid coolers are an open loop system, meaning they can be extended by adding more blocks and radiators as required, to accommodate installations where one or more CPUs and /or multiple graphics cards are present in the same enclosure. Other than this, the principle is exactly the same as with AIO liquid coolers: the coolant passes through each cooling block, transferring the heat to the coolant which is then cooled as it circulates through a radiator.
Size Matters
Since an air cooler’s effectiveness is determined by the amount of surface area it offers, the larger the cooler and the more fins, the better it can cool, and since air coolers come as a single unit, this can make some air coolers quite bulky. If space is limited, as in the case of small footprint or small form factor enclosures, it can be difficult to comfortably mount them to the processor without bumping into nearby memory modules, wiring, or other cards and components.
Learn More: Types of Computer Cases and Their Form Factors

Liquid coolers in comparison, come in a split configuration with separate cooling block and radiator units, interconnected with tubing. The cooling block, which is mounted on the processor, has a low profile, and can therefore fit more easily when space is tight. The radiator can then be suitably mounted anywhere else within the enclosure.
Ease of Installation
The actual installation process is more complicated in the case of liquid cooling solutions, especially with custom loop liquid coolers. AIO liquid cooling installation is only slightly more complex than with a standard air cooling solution, but custom loop liquid coolers require a reasonable level of technical knowledge and expertise, as well as some planning and are therefore mostly aimed at enthusiasts.
Heat Expulsion
An important factor to consider on both air cooled and liquid cooled solutions is what happens to the dissipated heat. With a liquid cooled solution, the radiator and fan are mounted on the chassis where the dissipated heat can be directly expelled and is not recirculated within the enclosure. This can make liquid cooled solutions even more efficient than air cooled.
With air cooled solutions, the air drawn across the fins is usually recirculated within the enclosure and another fan or fans, mounted to the chassis are relied upon to expel the air from inside the enclosure. While airflow is an entire topic on its own, unless correctly positioned, multiple fans in the same enclosure often work at cross purposes, with fans vying for the same pocket of air, one to draw air across the heatsink fins, the other fighting to expel it.
Use Cases
Unless a system is running close to or above its maximum specification temperatures, an air cooled solution is often the easiest, cheapest, and most reliable option, having only a single moving part, the fan. It is also the simplest to maintain with the only expendable component being the fan, which is cheap and easy to replace.
However, if for whatever reason, more effective cooling is required, AIO liquid cooling is an excellent option. It is quieter than an air cooled solution, and offers more efficient cooling, making it ideal for overclocking or on systems running processing intensive applications, while still being reasonably easy to install.
Finally, a custom loop liquid cooled solution is ideal in cases where a system needs to effectively cool several processors simultaneously, where there are more than one CPUs and/or GPUs.
Conclusion
Air cooled solutions are very common, comparatively easy to install, and low cost. They offer more than adequate cooling under normal conditions. Liquid cooled solutions are slightly more effective at absorbing and transferring heat away from the processor, due to the coolant’s higher thermal conductivity compared to a metal heatsink, and are therefore better suited for high performing systems that must endure continuous and extreme processing loads.